Occupational Health and Safety
Challenges and Commitments
Labor is a crucial factor in enhancing an organization’s capacity for sustainable business operations. Therefore, GGC is committed to developing employee capability. In addition, GGC places great emphasize on human rights risks, which are globally recognized concerns. To prevent adverse impacts on the company's operations from such risks, GGC is committed to managing safety in all of its operations, covering both safety in the production process and personal safety in accordance with national and international standards such as United Nations Guiding Principles on Business and Human Rights: UNGP that publish in 2011, to reduce the risks that may occur and promote equal treatment in accordance with human rights principles as well as preventing the loss of life, property, reputation of the Company, negative impacts on the community and the environment caused by accidents or incidents that may occur from its operations.
Key Stakeholders
Employee
Supplier and Business Partner
Customer
Goals
process accidents is
0
in 2024
process accidents is
0
0 in 2024
Frequency Rate (LTIFR) is
0
in 2024
Management Approach
5-Year Occupational Health and Safety Strategy (2020-2024)
GRI 403-1 (2018), 403-2 (2018)
Personal Safety
|
|
Process safety
|
|
Off the Job Safety
|
|
Emergency/ Crisis Management
|
|
For more details about the Health and Safety Performance, see Performance Data 2024
Duties of the Occupational Health and Safety Committee (SHE) GRI 403-4 (2018)
GGC has established the SHE Steering Committee to supervise and monitor the operation in accordance with the Company's internal safety, health and environmental standards, to meet international standards, and achieve the goal of being an accident-free organization. GGC has also set up an Occupational Health and Safety committee, which consists of representatives from employees to open channels for consultation with and participation of workers, and workers' representatives, as well as monitoring and evaluating SHE performance of related agencies. The progress of its operations is reported monthly.
1. Set and review policies, goals, plans for SHE.
2. Supervise, support and follow up on the SHE performance of relevant departments to operate according to international standards and consistent with the Company's policy.
3. Consider, approve and publish the SHE manual and key processes, covering the operations of the Company.
4. Hold a meeting of the SHE Board of Directors at least 6 times a year.
5. At the meeting, there shall be a quorum of not less than 50%.
6. Appoint sub-committees or working groups as necessary and appropriate.
Process Safety GRI 403-3 (2018)
GGC has applied Process Safety Management (PSM) as a standard for operations in the factory area and implemented the Plant Reliability Master Plan to ensure that production operations can continue to operate efficiently with maximum safety. In addition, the safety management in the production process is audited by external auditors. Furthermore, GGC has set additional risk mitigation measures to prevent the severity of the risks that may be encountered during operations, as well as the stability and performance management system of the machine production efficiency control and risk mitigation measures to reduce the likelihood of unsafe events, etc.
GGC has developed the efficiency of its safety potential, as well as maintained operational standards to be able continuous safe production by establishing production process safety projects such as:
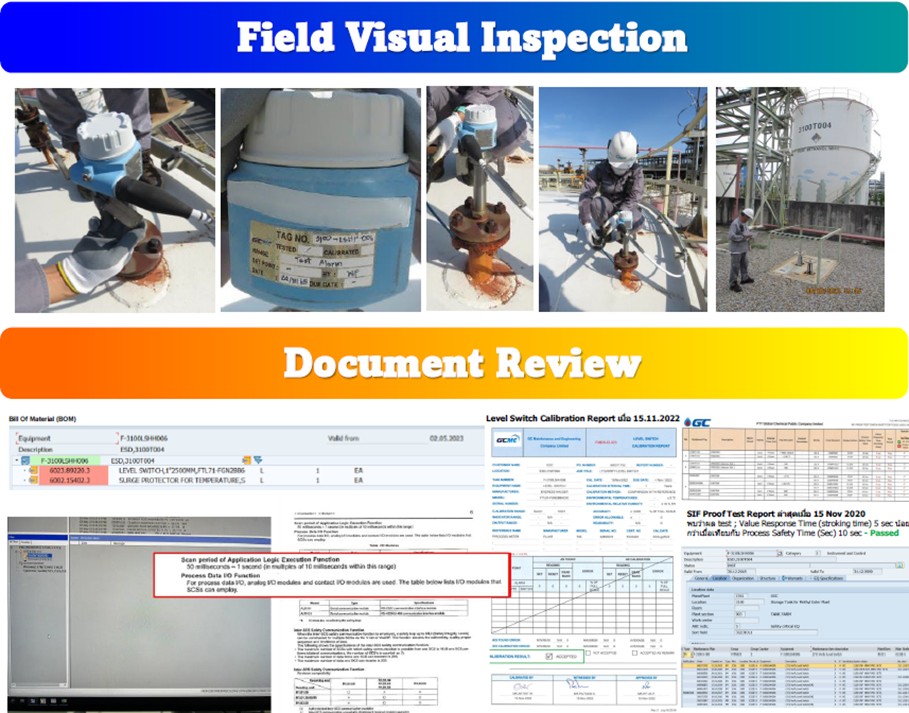
Bow-Tie Barrier Validation Checklist Project GRI 403-2 (2018)
GGC has applied Bow-Tie risk identification to monitor process safety accidents. The Bow-Tie is used as a tool to verify various barriers used to prevent and mitigate the impacts of Major Accident Event (MAE) of the plant. The Company reviews the Preventive Maintenance (PM) of protective equipment in conjunction with actual on-site inspections. The Bow Tie Validation allows GGC to categorize the actions that have been observed into 2 categories, which are Actions that align with the Standards and Actions that are needed to be improved. In case of defects, relevant departments are responsible for considering and revising the relevant issue in order to return to work effectively as usual. This can prevent serious accidents and reduce interruptions in the production process. In addition, the obtained results have been used to continuously improve and develop systems and safety control standards in preparation for emergency situations that may occur both in the present and in the future through the integration of actions to prepare for and respond to emergency situations. In 2024, the company conducted a risk identification assessment for its two plants in Rayong and Chonburi provinces. This year’s risk identification includes activities such as evaluating the effectiveness of the Methanol Leak to Storm Water System to Outside Plant Boundary to prevent leaks into external water sources.
Field Risk Assessment (FRA) & Smart SWO Project GRI 403-2 (2018), GRI 403-7 (2018)
GGC has assigned relevant employees to conduct on-site inspections to assess the condition and readiness of production and safety equipment. Employees are required to check the operational readiness of the equipment, prepare inspection reports, and identify areas for improvement or potential enhancements
In 2024, GGC has conducted inspections on safety-related systems in the following areas:
- Inspection of fire equipment cabinets and fire hoses used for water and foam discharge in case of a fire.
- Inspection of the operational mechanism of Fixed Monitors according to the PIP sequence, ensuring they can rotate in all directions as required and effectively discharge water and foam in case of a leakage.
- Inspection of Fire Water systems used for cooling around storage tanks in case of a fire.
- Inspection of the operational mechanisms of the Foam System and Foam Chamber.
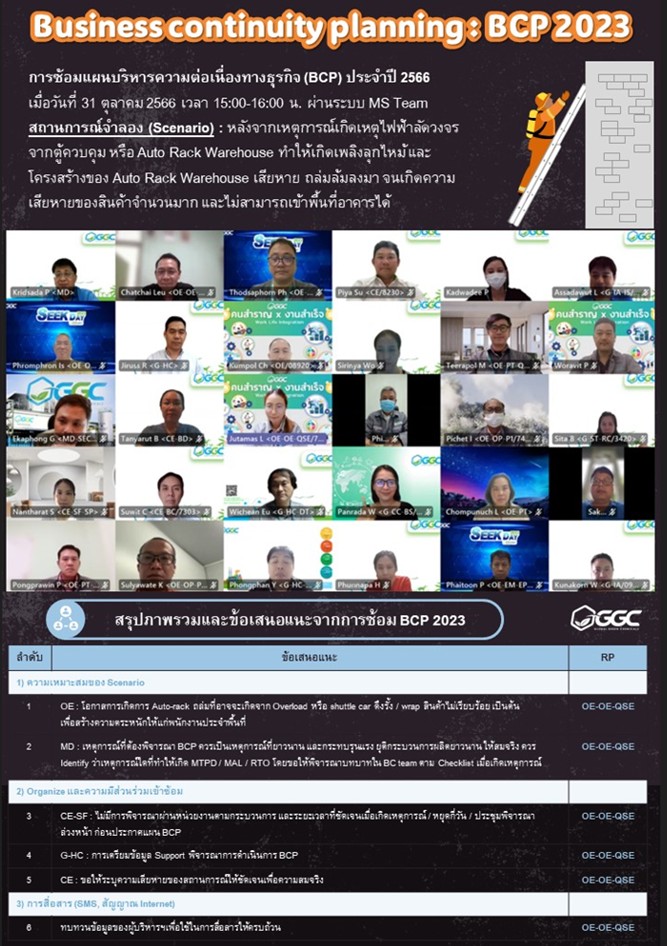
Business Continuity Plan (BCP) Project GRI 403-5 (2018), 403-7 (2018)
GGC conducts an annual Business Continuity Plan (BCP). The objective of the training was to enhance understanding of the roles, duties, and responsibilities of each department, rehearse the response strategies of each department, and coordinate collaboration to minimize errors in real-life scenarios. In the event of an emergency, the drills specify the responsibilities of each department, outlining the actions to be taken and the departments with which they need to coordinate.
In 2024, two drills were conducted:
- A scenario was established related to the production process that required a physical response plan. This involved a fire response simulation at the Compressor in the Fatty Alcohol Unit, which took place in April.
- A scenario was created to practice resolving business operations issues in the event of a business disruption. The issue simulated was the damage to the Crankcase, Crankshaft, and Cylinder in the production process.
The drills involved relevant departments, including the Finance Team, Corporate Affairs Team, Human Resources and Corporate Support Team, Operations Team, Strategy and Commercial Team, and Safety and Environment Team. Each team was required to discuss reporting data, coordination procedures, timelines, and relevant departmental content to ensure a timely and effective response to business disruptions.
Benefits from the Programs
- 51 employees participated in the project.
- The company can manage and respond to risks appropriately and promptly.
- To respond to emergencies and minimize their impact on business operations.
- The BC Team understands their roles, duties, and responsibilities.
- Relevant departments can take immediate corrective actions and collaborate to train and coordinate strategies, enabling the company to sustain its operations continuously
e-Permit to work (e-PTW)
GGC launched the e-Permit to Work (e-PTW) project at its Rayong and Chonburi facilities, with implementation beginning on 18 July 2023. The system has been continuously used to enhance the efficiency of work permit requests, making the process more convenient and reducing approval time. It also facilitates inspection and monitoring, as all data is recorded online, allowing for remote approvals anytime, anywhere. For contractor work approvals, the system automatically retrieves contractor data from the database, including safety and occupational health training records, confined space training, and various work skills, minimizing errors in information verification. Also, e-PTW features a dashboard that clearly displays approved work types, enabling more efficient data collection. This data can be leveraged for operational performance assessments and tracking high-risk work categories related to occupational health and safety.
Personal Safety GRI 403-2 (2018)
GGC promotes safety culture to raise awareness of personal safety to employees and contractors, as well as sets various tools to drive the creation of a continuous safety culture, such as organizing 5S activities, organizing a safety committee meeting to report on the progress of safety operations on a monthly basis, accident risk reporting, continuous SWO (Safety Walk Observation) activities, and establish standards/safety procedures, etc.
However, accidents can still occur. Severe incidents may affect GGC's image and safety goals at a high level. GGC has, therefore, established a risk mitigation plan and personal safety promotion program to reduce the severity of such events as follows:
Raising Safety Awareness
GGC continues to raise awareness of safety and strengthen the management of necessary standards for production personnel at all levels on a regular basis, consisting of: Process Safety Management according to lawful standards, Reducing energy consumption in production, Promoting safe work discipline, and Waste Reduction.
Understand Risk Project
GGC has organized the Understand Risk Project to promote knowledge and understanding of safety and the risks involved in the work process for operators and contractors through conversation and performing OHS risk and hazard assessments to identify what could cause harm in the workplace, as well as test their knowledge on the steps to prevent the risk correctly. If it is found that operators’ knowledge and understanding of risk identification and the prevention of such risks is insufficient, GGC will provide additional training on how to properly and appropriately prevent risks that may occur in the future. From the implementation of the project, it is found that Employees have always been aware of the risks and safety issues in their operations.
Safety Walk Observation (SWO) Project
GGC has continued the SWO project since 2013 to create a safe culture in the organization by encouraging executives at the Vice President level to lead the team to observe the performance behavior of all employees and contractors in the production process through walks to perform Internal Inspection of activities and risky behaviors, as well as the safety of machinery and equipment within the work area on a regular basis of 5 days a week for 15 minutes, in order to record data and converse and discuss with employees if unsafe behavior is identified in the work area. The inspecting executive can complement employees when working safely or give warnings when encountering unsafe operations. The data is reported at the Operation Committee Meeting (OCM) every working day or to the Safety Committee (OAC) every month.
3 Brave Man
The company implemented the "3 Bravery" initiative to enhance safety awareness among employees and contractors. In 2024, the company emphasized the "Brave Man Stand Up" principle, encouraging the courage to improve and optimize existing practices. As part of this initiative, the company organized a video competition under the theme "3 Bravery"—Dare to Stop, Dare to Warn, and Dare to Ask. Employees were invited to create and submit videos showcasing different perspectives on safety through acts of courage. The winning video will be used as a promotional tool for internal safety campaigns and personal safety awareness. To further motivate participation, the company provided awards to the winners. A total of XX participants joined the competition, with five winning teams receiving a combined cash prize of 6,500 THB.
Safety Commitment Workshop
To enhance knowledge and understanding of occupational health and safety among both internal and external personnel involved in production, the company organized the Safety Commitment Workshop. The workshop aimed to engage contractor executives in discussions on Safety KPIs and reinforce their commitment to achieving a zero-incident workplace. This was done through effective safety communication within contractor teams and employees. Furthermore, the workshop provided training and guidance on managing Plant Shutdown procedures in alignment with the 5R principles, ensuring a shared understanding and minimizing the risk of accidents or operational disruptions. In 2024, the company successfully conducted the program, achieving 100% contractor participation.
Refresh SHE Procedure Regulation and PSM Awareness Training Program
The company’s SHE Committee conducts annual training sessions to reinforce knowledge and understanding of Process Safety Management, Chemical Management, and Waste Management. These sessions are delivered through the company’s Green Learning (TPM) system to raise awareness and encourage employees to comply with safety regulations and environmental best practices. To boost participation, the company offers incentives, awarding prizes to the first 40 employees who demonstrate dedication, discipline, and commitment to attending the training.
GGC QCC Connected Minds Project
GGC has launched the QCC Connected Minds initiative, offering employees the opportunity to collaborate on projects that integrate technology to enhance organizational quality and align with the Zero Incident Target related to incidents, complaints, and unplanned shutdowns. Interested employees can submit projects that must follow the QCC framework, including situation analysis, KPIs, project timeline, root cause identification, solution selection, monitoring and evaluation, and standardization. All project proposals must be approved by the Division Manager. Winning projects will be awarded and presented at the upcoming GC SEEK DAY for further recognition.
One Supervisor One B-CAREs GRI 403-7 (2018)
GGC is committed to fostering participation in workplace safety among supervisors, employees, contractors, and other relevant units. The approach emphasizes Engineering Control to eliminate hazards at the source and establish a Safety in Line Responsibility culture. Supervisors of employees and contractors are encouraged to submit their own workplace safety improvement projects for a competition. This initiative aims to strengthen the company's safety culture, enhance safety awareness, and promote innovative thinking regarding safe work practices. In 2024, the company continues this project from the previous year, with a focus on the Brave Man Stand Up principle—encouraging the courage to develop or improve existing practices for greater efficiency using technology. Submitted safety projects must either be newly developed or completed within the past two years. This initiative will not only reinforce the company's safety culture but also foster strong relationships among supervisors, employees, and contractors.
B-CAREs KYT Project
GGC has organized the B-CAREs KYT project to create participation in worker safety and a culture that emphasizes participation in on-site hazard analysis, as well as anticipating potential dangers and setting measures to manage those hazards to ensure safety for all workers through the Clip VDO B-CAREs KYT contest.
OHS Program GRI 403-2 (2018), 403-4 (2018), 403-5 (2018), 403-7 (2018)
|
|
|
|
|
|
|
|
|
|
|
|
|
|
Promotion of Worker Health GRI 403-3 (2018), 403-6 (2018)
GGC is aware of the importance of taking care of the health of its employees. Therefore, GGC provides a health check-up for workers working on high-risk duties by qualified physicians as required by law. The first check-up must be completed within 30 days from the employee’s starting date. The next check-up is at least once a year. In case of absence from work for 3 consecutive days due to danger or illness, abnormality, or the operator may have an illness due to working for GGC, employees will be treated immediately. GGC, then, investigates the cause of the abnormality to prevent further issues. The health check-up results must be strictly kept confidential in accordance with the Company’s privacy policy.
In addition, the Company has implemented various projects to maintain the health and well-being of its employees. For more information, see Our Employee